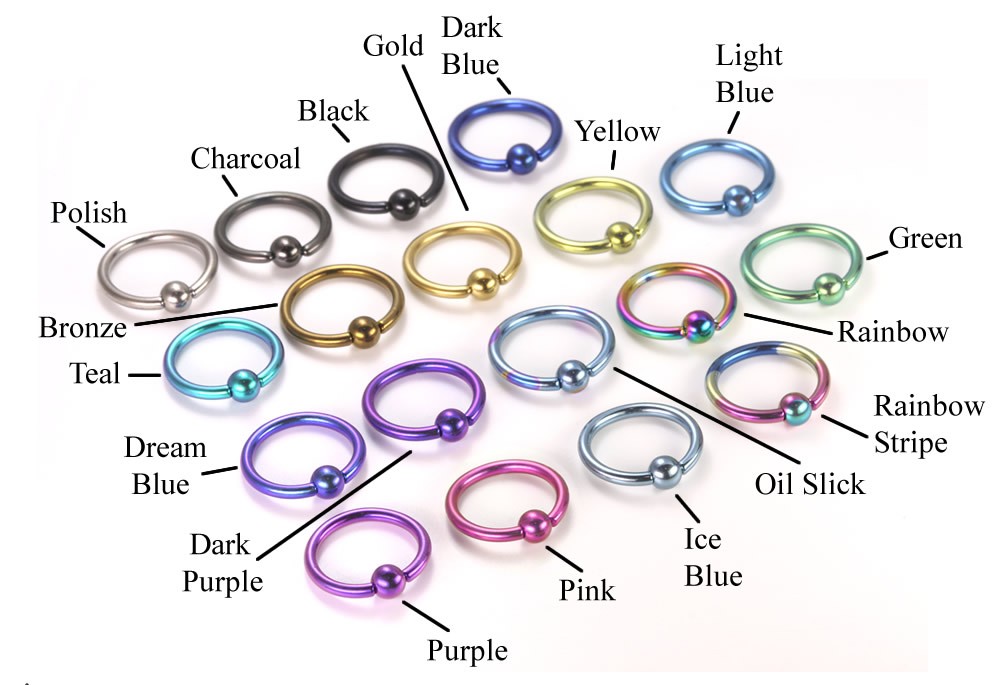
Anodizing is an electrochemical conversion process that forms an oxide film, usually on aluminum, in an electrolyte (chemical solution). The aluminum parts are the anode (thus the term “anodizing”) and current is passed between them and a cathode, usually flat aluminum bars, through the above mentioned electrolyte (sulfuric acid is most commonly used). There are different types of anodize, most commonly referred to as Type I-Chromic Acid Anodize, Type II-Sulfuric Acid Anodize, and Type III Hard Anodize or Hardcoat from the Mil-A-8625 designation. Other less common types are phosphoric acid and titanium anodize. The anodize is a porous structure that grows out of the base aluminum and absorbs colored dye very well. This is done through a secondary operation with either an organic or inorganic coloring. Anoplate processes black, blue, red, gold, as well as small lots of green and gray using standard organic dyes. We also do electrolytic coloring (Anoplate’s AnoBlack EC & EC7) which produces a gray-black color using inorganic metallic salts. Any colored anodize is required to be sealed following processing in order to preserve the color.